3D Printing Arizona transforms CAD models into physical objects using a layering process. It can produce everything from one-off concept models to functional prototypes and bespoke production runs for testing.
It can also replace traditional manufacturing processes in low to mid-volume applications like tooling and end parts. BMW used 3D printing to create an optimised roof fixture that weighs 44% less than a machined version.
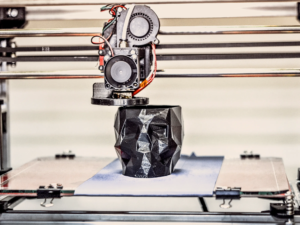
As the name suggests, rapid prototyping is the process of rapidly turning a digital CAD file into a tangible object. This allows teams to test out new designs without having to invest significant time and resources into a final product.
This technology can save companies a great deal of money and lead to more innovative products. Oftentimes, it can even eliminate the need for costly warehouse storage or shipping and handling costs associated with traditional manufacturing.
The ability to quickly create prototypes also means that there is less time needed for iterations, which in turn results in a more effective design. For example, a team may be able to change the placement of an element or remove an unnecessary feature. This can improve ergonomics and functionality and help ensure that the final product is user-friendly.
3D printing can also be used to create more complex geometries that would be difficult or impossible to manufacture using other methods. For example, it is possible to create parts with internal lattice structures that increase strength and reduce weight. This can have significant implications in aerospace and automotive applications. It is also possible to create components with internal cavities and voids for use in medical care, such as prosthetics and implants.
While there are many different rapid prototyping processes available, it is important to choose the right one for your project. To begin with, it is important to set a clear goal for the prototype, such as validating an idea or testing usability. Then, consider the different stakeholders involved in the project. It is important to include them early in the process so that they can provide valuable feedback and contribute to the final decision.
Once you have determined your goals, it is important to choose the right materials for the prototype. For example, polymer plastics are commonly used for low-fidelity prototypes, while ceramics are ideal for high-strength and heat-resistant applications. For higher-fidelity prototypes, you can choose from a variety of resins that offer excellent detail and surface finish. You can even use metals for functional testing and short-run production, such as Selective Laser Melting (SLM) or Direct Metal Laser Sintering (DMLS). Multi Jet Fusion, developed by HP, uses an inkjet array to apply fusing and detailing agents across a powder bed to create robust, detailed parts.
Additive Manufacturing
The process of 3D printing involves transforming a digital CAD (Computer-Aided Design) file into a three-dimensional physical solid object or part. It works by applying material layer-by-layer. The layers may consist of a powder bed with binder materials or solid plastics like those used in consumer-grade printers. The layers are melted or fused together using an external heat source such as a laser or a printhead in the case of polymer-based systems. Often, the finished product requires a post-print treatment such as painting or curing to achieve the desired appearance and performance of the part.
The technology is so versatile and powerful that it is already a significant production process for many companies. In addition to its ability to produce complex geometries that would be difficult and expensive to make with conventional subtractive manufacturing methods, it allows for a greater degree of flexibility in the design of the final product. This means a product can be produced in its entirety or with removable features that allow it to be disassembled and shipped in parts to be assembled at a later time, thus lowering overall costs and allowing for more rapid product development.
In its most sophisticated form, it can be used to create medical implants and tools for the repair or replacement of damaged body structures. Physicians can use 3D printers to make prosthetics and hearing aids, artificial teeth and bone grafts. Researchers can replicate models of tumors or other internal bodily organs from CT scans to guide surgery or other medical procedures. In addition, there are plans to develop machines that can print living tissues such as kidneys or blood vessels for transplants.
For consumers, the technology is being used to make toys, jewelry, art objects, phone cases, lamps, tables and tools. It is also being used by designers to quickly turn ideas into models that can be examined for form, fit and function, and by archaeologists to reconstruct damaged or rare artifacts. It is even possible for people in remote locations to set up domestic 3D printers and fabricate a wide variety of items themselves.
Customization
Unlike traditional manufacturing, which requires specialized tooling to produce a product, 3D printing is an entirely digital process. This eliminates the need for molds and reduces upfront costs and time to market. Additionally, manufacturers can quickly iterate and modify designs, providing users with customized products to meet their design preferences and functional requirements. This allows companies to stand out from competitors and boost customer loyalty.
3D printers use a variety of technologies to print objects, with the most popular being fused deposition modeling (FDM) and fused filament fabrication (FFF). FDM uses a heated extrusion nozzle to deposit layers of material in layers that build up the object. Most consumer and home printers use FDM, which produces an array of objects ranging from ornamental to practical applications such as backscratchers, coat hooks and doorknobs.
The flexibility of 3D printing opens new possibilities for designers and engineers. Using 3D printing, manufacturers can create complex parts with intricate geometries that would be impossible to make with conventional production methods. This freedom of design provides the foundation for innovative, customizable products that set businesses apart from their competitors and increase differentiation in a crowded marketplace.
While most companies use 3D printing to support their existing production processes, it’s increasingly being used as a standalone manufacturing technology for end-use parts and products. The technology can produce complex geometries in a wide range of materials, from high-temperature thermoplastics to composite filaments to stainless steel. This provides significant flexibility and enables manufacturers to reduce lead times, shorten production run times and lower costs without sacrificing quality or strength.
In the automotive industry, 3D printing can be used to produce customized car parts for individual drivers. For example, Ford has created a platform that allows owners to 3D print custom accessories that customize the interior and exterior of their vehicle. In addition to personalization, these customizations can enhance vehicle performance and safety.
Medical professionals are also leveraging 3D printing for mass customization to improve patient outcomes. Custom prosthetics and orthotics can be produced to fit an individual’s unique anatomy. This provides better care and improved outcomes for patients while reducing costs to the healthcare system.
Sustainability
The 3D printing process is a greener alternative to traditional manufacturing methods, which can produce substantial waste and consume large amounts of energy. This technology allows companies to manufacture products locally, cutting costs and carbon emissions. In addition, it can create products with a smaller footprint and can eliminate the need for tooling and molds, which require significant energy to produce.
The process starts with a virtual design, which is made using computer-aided design (CAD) software. It works much like a blueprint for the printer to read and turn into an actual object. This type of software is used for many applications, including aerospace design, vehicle production, and medical devices. Using this software allows designers to make adjustments in minutes, significantly improving the efficiency of the production process. In contrast, it would take hours to make minor changes in a conventional injection molding machine.
Next, the raw material is loaded into the 3D printer. This can be a variety of materials, but the most common is plastic. It is important to select a biodegradable, eco-friendly resin that minimizes your environmental impact. This can be done by utilizing recycled plastics or choosing a renewable, plant-based resin such as PLA (polylactic acid), which is made from corn or sugarcane.
After the object is printed, it is removed from the machine and is cleaned and labelled before being sent to recycling centers or upcycled into new items. It is important to label the resin scraps so they are properly processed and redirected from landfills, as they can otherwise be contaminated with other materials. 3D printers that utilize SLS technology are able to recycle unused resins, and Nexa3D has a number of options for upcycling resin scraps into new parts.
Shipping raw materials and finished goods over long distances is a huge contributor to a company’s carbon footprint. By creating the products locally, companies can cut their transportation and carbon footprints drastically. This also enables them to produce their products on demand, which can help them reduce stock and inventory levels and save money.
In the future, we can expect 3D printing to be used in a wide range of environmental applications. This includes applications for air quality, water and energy, and separation devices.